Experiment
TD1007
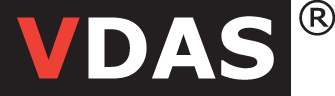
WATER TO AIR HEAT EXCHANGERS
An experimental unit to show how cross-flow water to air heat exchangers work.
If you have any questions or you'd like to discuss a product, please call us.
+44 1159 722 611WATER TO AIR HEAT EXCHANGERS
Many thermodynamic applications use water to air heat exchangers. Examples include using circulated water to heat or cool air in a HVAC installation, or to cool hot water using a flow of air, as in the radiator of a combustion engine.
The TecQuipment Water to Air Heat Exchanger mirrors air heating and water cooling applications. It fits on a bench top and includes a hot water supply, a cooling air duct and all instruments needed for tests on cross-flow heat exchangers. The heat output of the design produces good results without greatly affecting the temperature of a reasonable size classroom or laboratory.
It’s hot water system includes a tank with a PID controlled electric heater for stable temperatures, a pump and tank level indicators. An electrically operated valve opens to let water in to fill the tank. The tank has protection in case of over temperature, low water level and overfilling. A precision needle valve and flow meter control and measure the water flow rate.
The cooling air passes down a vertical duct containing an orifice plate which connects to a differential pressure transducer. The air then passes through a fixed speed centrifugal fan and along a horizontal duct containing the heat exchanger. The air exits the duct through a handoperated slide-valve. Students use the orifice and valve to measure and control the air flow.
Thermocouples at the water connectors and in the air duct measure hot and cold inlet and outlet fluid stream temperatures. Clear, multiline digital displays show the temperatures, water flow rate and orifice pressure (to calculate air flow).
For safety and simplicity, the heat exchangers have selfsealing quick connectors for their water supply. Quick release clamps and locating dowels hold the heat exchanger in the air duct. Students need no tools to fit and change the heat exchangers.
Each heat exchanger includes a mimic diagram that attaches to a space on the main unit panel. The diagram gives useful information to the student, including how to connect the heat exchanger. Each heat exchanger has transparent sides so students can easily see their construction and understand how they work.
The equipment includes one heat exchanger as standard. It has 32 tubes in two banks of 16, allowing the addition of a thermocouple at the mid point. TecQuipment supply two different heat exchangers as optional extras. One (TD1007a) has a single bank of 16 tubes, giving half the heat transfer area of the standard heat exchanger. The other (TD1007b) also has a single bank of 16 tubes, but includes fins to increase the heat transfer area to equal that of the standard 32 tube heat exchanger.
The different heat exchanger options give students a better understanding of how they work and how size and construction may affect practical applications.
The equipment includes a space for TecQuipment’s optional VDAS-F. You can do tests with or without a computer connected. However, for quicker tests with easier recording of results, TecQuipment can supply the optional Versatile Data Acquisition System (VDAS®). This gives accurate real-time data capture, monitoring and display, calculation and charting of all the important readings on a computer.
Learning outcomes
- Heat transfer between fluids through a solid wall
- Energy balance and efficiency
- Finding the heat transfer coefficient and Log Mean Temperature Difference (LMTD)
- Effect of water temperature (the ‘driving force’)
- Comparing actual midpoint water temperature with the average based on overall inlet and outlet temperatures
- Comparing temperature change between upstream and downstream tube banks
- Comparison of heat exchangers of different construction and heat transfer area (needs optional TD1007a and TD1007b)