Experiment
TM164
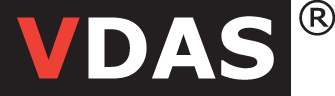
FREE VIBRATION OF A MASS SPRING SYSTEM
An experimental apparatus that shows students the oscillatory motion of a mass-spring system in terms of both displacement and acceleration.
If you have any questions or you'd like to discuss a product, please call us.
+44 1159 722 611FREE VIBRATION OF A MASS SPRING SYSTEM
This product is part of a range that explores free vibrations in simple ‘one degree of freedom’ systems.
It introduces students to key scientific terms such as:
- Simple harmonic motion (SHM) and frequency of oscillation
- Spring constant and Hooke’s Law
- Oscillation damping
- Phase difference between displacement and its derivatives
This product fits to the sturdy Test Frame (TM160)for study or demonstration.
The mass-spring system is one of the most easily explainable oscillatory systems. This is because students may already be familiar with Hooke’s Law, showing the force exerted by a spring is proportional to the extension. Therefore, students can easily make the link to simple harmonic motion - defined as the oscillatory motion where the restoring force is proportional to the displacement. A back panel fixes to the Test Frame. The panel holds two vertical guide rods and a non-contacting displacement sensor. A test spring suspends a balanced mass platform which vibrates (oscillates) vertically in the guide rods. Students fit additional masses to the platform, and a second spring is provided to test various system combinations.
The displacement sensor measures the vertical oscillations of the platform. An additional sensor (accelerometer) built into the platform measures the acceleration of the platform as it moves up and down. Both sensors measure the motion, yet create negligible damping.
The back panel has a printed scale. Students use it with a cursor on the platform to measure accurately the spring extension, to show Hooke’s Law and find the spring constant.
Students pull the platform gently down and release, allowing it to vibrate. They then find the frequency of oscillation and compare it with that predicted from theory. TecQuipment calibrate the sensors to work with VDAS® (mkII) for real-time display and data acquisition of system oscillation wave-forms. Students use the software to see both the displacement and acceleration wave-forms to confirm the phase difference between them and measure frequency. The software calculates and shows the first two derivatives of displacement - velocity and acceleration. Students can then see and compare both the measured and derived acceleration at the same time, to confirm the relationship.
TecQuipment have specifically designed the TM164 to work with VDAS® (mkII). However, the sensor outputs may be connected to your own data acquisition system or oscilloscope if desired.
Students may fit an optional Damper Kit (TM164a) to test how viscous damping affects the system oscillations. This simple piston disc and cylinder form a dash-pot damper that fits to the guide rods under the platform. It works with easily found non-toxic fluids (not supplied) for different damping levels. For example: water and vegetable oil will produce light damping, while castor oil produces heavy damping. Students may try their own fluids (provided they are safe and do not damage the equipment) and their own piston discs for project work. When using the Damper Kit, VDAS® can fit its displayed data to underdamped and overdamped viscous damping models.
Note: You may purchase any number of damper kits to make the change between the various fluids more convenient.
Learning outcomes
- Spring extension and force (spring constant), and Hooke’s law
- Frequency of oscillation, spring constant and varying mass
- Phase difference between displacement and its derivatives
- Comparison of measured and derived acceleration
- Oscillation damping and coefficient (needs optional Damper Kit)